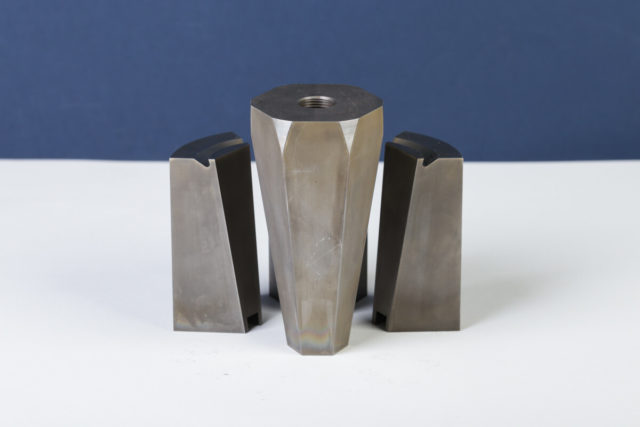
Stal narzędziowa w obróbce materiałów – rodzaje i zastosowanie
Stal narzędziowa to do tej pory najlepszy rodzaj materiału do obróbki, gwarantujący wysoką jakość wykonania. Stosuje się ją przede wszystkim do produkcji narzędzi przeznaczonych do ciągłej pracy, wymagającej dużej wytrzymałości i odporności. Jakie są jej zalety?
Przewaga stali narzędziowej nad tworzywami sztucznymi
Chociaż ciągle trwają badania nad tworzywami sztucznymi, zmierzające do ich ulepszania, trudno porównać ich możliwości do stali narzędziowej. Szczególnie pod kątem trwałości i wytrzymałości, która w przypadku tej ostatniej, jest wielokrotnie wyższa. Przewaga stali narzędziowej powoduje, że to właśnie ona stanowi najlepszy materiał do produkcji narzędzi służących obróbce i skrawaniu tworzyw sztucznych.
Zastosowanie stali narzędziowej według rodzaju
Wśród stali narzędziowych wyróżniamy kilka jej rodzajów:
- stal narzędziową niestopową,
- stal do pracy na zimno,
- stal do pracy na gorąco,
- stal szybkotnącą.
Ich użycie różni się w zależności od zastosowania i przeznaczenia wytwarzanego narzędzia.
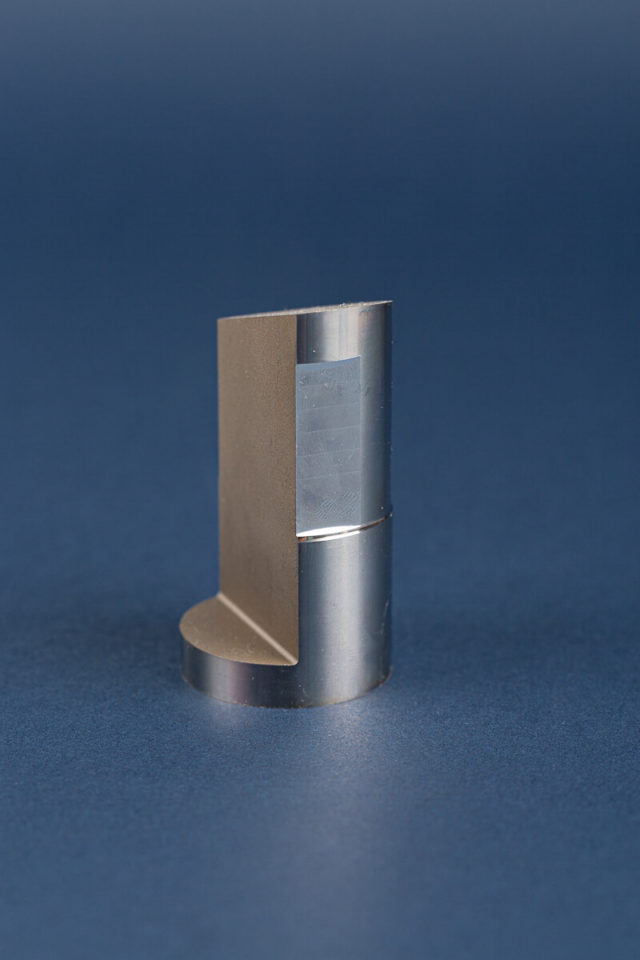
Stal narzędziowa niestopowa – zastosowanie
Do wyrobu narzędzi o prostych kształtach, jak młotek, siekiera, wykrojniki czy przebijaki wykorzystywana jest stal narzędziowa niestopowa, dawniej nazywana węglową. Ten rodzaj stali jest pozbawiony dodatków stopowych i innych pierwiastków. Zawiera tylko węgiel, który zwiększa twardość materiału i odporność powierzchni na ścieranie. Stale niestopowe posiadają małą hartowność, ich rdzeń jest bardziej miękki i ciągliwy, co pozwala stosować ją na narzędziach narażonych na dynamiczne obciążenia. Do narzędzi pracujących udarowo wykorzystuje się stal niestopową o niższej zawartości węgla. Stale o dużej zawartości węgla stosowane są przy produkcji narzędzi do obróbki metali z niewielką szybkością skrawania. Należą do nich m.in.: frezy, wiertła, narzynki, gwintowniki.
Stal do pracy na zimno i gorąco – zastosowanie
Dla elementów, których produkcja nie wymaga wysokiej temperatury, stosowana jest stal do pracy na zimno. Chodzi tutaj o temperaturę powierzchni narzędzia podczas pracy. W przypadku „zimnej” obróbki nie powinna ona przekraczać 200 st. C. Stale przeznaczone na narzędzia do pracy na gorąco mogą osiągać wyższą temperaturę, natomiast największe możliwości w tym zakresie oferuje stal szybkotnąca. Obróbka skrawaniem i formowanie przy jej użyciu mogą nagrzewać się nawet do temperatury 600 st. C.
Stale do pracy na zimno, w porównaniu ze stalami niestopowymi, mają zwiększoną hartowność i podwyższoną odporność na ścieranie. Świetnie sprawdzają się więc przy produkcji większych narzędzi o bardziej skomplikowanych kształtach. Stale narzędziowe do pracy na gorąco odznaczają się natomiast własnościami mechanicznymi w podwyższonych temperaturach i dostateczną odpornością na szybkie zmiany temperatury.
Stale szybkotnące – zastosowanie
Stale szybkotnące stosowane są w produkcji narzędzi skrawających, pracujących w bardzo ciężkich warunkach, dużych szybkościach skrawania i dużych przekrojach wióra. Mają one wysokie stężenie węgla i dodatki stopowe: chrom, wolfram i molibden, wanad lub kobalt. Każdy z tych stopów pozwala uzyskać określone właściwości. Chrom, na przykład, zwiększa hartowność, zmniejsza szybkość utleniania i wzmacnia efekt twardości wtórnej. Wanad zwiększa odporność na ścieranie, a kobalt podnosi twardość w wyższych temperaturach i zwiększa przewodność cieplną.
Najważniejsze cechy stali narzędziowych
Stale narzędziowe służą do wytwarzania elementów i detali do rozdzielania, rozdrabniania, obróbki skrawaniem lub nadawania kształtu materiałom. Chociaż ich rodzaje różnią się w zależności od zastosowania, stale narzędziowe muszą spełniać cztery podstawowe wymagania:
- Wysoka twardość.
- Odporność na ścieranie.
- Odpowiednia hartowność.
- Odporność na działanie podwyższonych temperatur.
Tylko kiedy te wszystkie warunki są spełnione, narzędzia wykonane ze stali narzędziowej mogą efektywnie spełniać swoje funkcje. Inne ważne parametry, na które trzeba zwrócić uwagę, to stabilność wymiarów, odporność na korozję i obciążenia dynamiczne – w zależności od przeznaczenia wytwarzanego narzędzia.
Chcesz mieć pewność, że Twoje maszyny są wyposażone w narzędzia o odpowiednich parametrach? Skontaktuj się z nami.