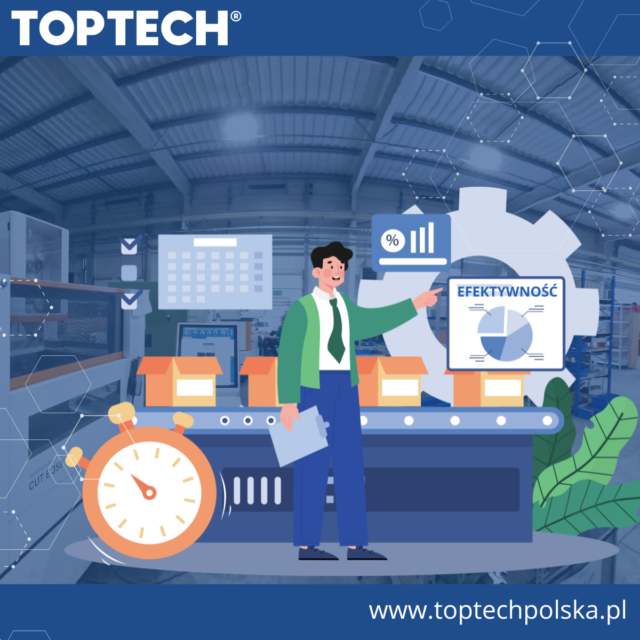
JAK ROZWIJAĆ EFEKTYWNOŚĆ PRODUKCJI JEDNOSTKOWEJ MATRYC, STEMPLI I ZNAKOWNIKÓW STOSOWANYCH W TŁOCZNIKACH POSTĘPOWYCH I TRANSFEROWYCH.
Współczesna produkcja jednostkowa stawia przed przedsiębiorstwami liczne wyzwania związane z osiąganiem wysokiej efektywności, precyzji oraz terminowości. Rozwój technologii oraz rosnące wymagania rynku zmuszają do ciągłego doskonalenia procesów produkcyjnych, które powinny łączyć zaawansowaną automatyzację, optymalizację kosztów oraz utrzymanie najwyższych standardów jakości.
O produkcji jednostkowej
W produkcji jednostkowej, gdzie każde zlecenie jest unikalne, pojawia się szereg wyzwań związanych z efektywnością. Trudno jest precyzyjnie oszacować czas realizacji poszczególnych operacji, czas potrzebny na przygotowanie półproduktu oraz czas wykonania detalu na maszynie. W związku z tym, naturalnie nasuwa się pytanie: czy w takim razie praca nad efektywnością w produkcji jednostkowej matryc, stempli i znakowników ma w ogóle sens? Czy możliwe jest jej rozwijanie w środowisku, gdzie każdy element jest prototypem? Czy warto inwestować cenny czas w zbieranie danych i analizowanie procesów, skoro każdy detal jest niepowtarzalny? Czy nie jest to przypadkiem niepotrzebna strata zasobów, które mogłyby być wykorzystane w bardziej produktywny sposób? Jak to wygląda w praktyce w TOPTECH® i jakie kluczowe wnioski udało nam się wyciągnąć na przestrzeni lat?
Początki – nie było problemu z efektywnością, ale czy na pewno?
W początkowych latach działalności TOPTECH®, efektywność mierzyliśmy w sposób bardzo ogólny i uproszczony. W momencie, gdy zamówienie od klienta trafiało na produkcję, technolodzy i operatorzy wykonywali szereg zaplanowanych zadań, a finalnie gotowy produkt opuszczał zakład. Mierzyliśmy przede wszystkim czas, jaki upływał od momentu otrzymania zamówienia do momentu wysyłki gotowego wyrobu do klienta. Efektywność realizacji zamówienia zależała głównie od sprawności i doświadczenia zespołu operatorów i technologów, od jakości wykonania detalu, od niezawodności parku maszynowego oraz od minimalizacji przestojów związanych z awariami (efektywność pracy maszyn) . W małej firmie, gdzie jeden technolog zarządzał całością produkcji, taki model pomiaru i zarządzania efektywnością wydawał się akceptowalny, choć już wtedy zdawaliśmy sobie sprawę z jego ograniczeń i braku szczegółowości.
Narastający chaos – sygnał alarmowy
Wraz z rozwojem firmy, wzrostem liczby zatrudnionych technologów i operatorów, dotychczasowy model „wszyscy robią wszystko” przestał się sprawdzać. Efektywność realizacji zamówień zaczęła systematycznie spadać, terminy realizacji wydłużały się w niepokojącym tempie, a opóźnienia w dostawach stały się niechcianą normą. W pewnym momencie sytuacja stała się na tyle poważna, że blisko połowa naszej produkcji opuszczała zakład po umówionym terminie. Zaczęliśmy odczuwać narastający chaos, który negatywnie wpływał na morale zespołu i relacje z klientami.
Wdrożenie systemu zarządzania produkcją – eskalacja chaosu i rozczarowanie
W desperackiej próbie odzyskania kontroli nad sytuacją, zaczęliśmy poszukiwać kompleksowego rozwiązania, które pomogłoby nam zapanować nad chaosem, zoptymalizować procesy produkcyjne i zwiększyć efektywność. Po długich poszukiwaniach zdecydowaliśmy się na wdrożenie zaawansowanego oprogramowania do zarządzania produkcją. System ten obiecywał automatyczne planowanie kolejności zleceń, uwzględniając przy tym terminy realizacji, specyfikację operacji, dostępność maszyn i personelu oraz inne kluczowe parametry.
Obietnica automatycznego i inteligentnego planowania była niezwykle kusząca i dawała nadzieję na szybką poprawę sytuacji. Niestety, szybko okazało się, że system planowania produkcji wymaga ogromnej ilości szczegółowych danych wejściowych, których po prostu nie posiadaliśmy. Ponieważ każdy detal był unikalny i produkowany jednorazowo, nie mieliśmy historycznych danych, które mogłyby posłużyć do efektywnego planowania. Zakupiony system, choć zaawansowany technologicznie, nie spełnił naszych oczekiwań w specyficznych warunkach produkcji jednostkowej, a chaos, zamiast ustępować, zaczął się jeszcze bardziej pogłębiać. To była kosztowna lekcja pokory.
Moment przełomowy – decyzja o zmianie podejścia
Po wielu miesiącach frustracji i nieudanych prób, nadszedł moment przełomowy, w którym postanowiliśmy radykalnie zmienić nasze podejście do problemu. Zdaliśmy sobie sprawę, że tradycyjne metody planowania i zarządzania produkcją, które sprawdzają się w produkcji seryjnej, nie mają zastosowania w naszym przypadku. Planowanie w produkcji jednostkowej, gdzie każdy wyrób jest unikalny, wydawało się wręcz niemożliwe. Jak oszacować czasy realizacji poszczególnych operacji, skoro każdy detal jest inny i wymaga indywidualnego podejścia? Czy detal uda się wykonać dobrze za pierwszym razem, czy konieczne będą kosztowne poprawki i przeróbki? Czy technolog poprawnie zaplanuje wszystkie operacje, uwzględniając specyfikę materiału i wymagania klienta? Problemy zaczęły się piętrzyć, a my czuliśmy, że stoimy w miejscu.
Podjęte kroki – od teorii do praktyki
W obliczu narastających trudności, postanowiliśmy wziąć sprawy w swoje ręce i krok po kroku opracować własną metodologię zarządzania produkcją jednostkową. Ustaliliśmy, że pierwszym krokiem musi być oszacowanie czasu produkcji każdego detalu, nawet jeśli będzie to tylko przybliżona wartość. Zdawaliśmy sobie sprawę, że nie będziemy w stanie osiągnąć stuprocentowej dokładności, ale wierzyliśmy, że nawet szacunkowe dane pozwolą nam lepiej planować i kontrolować proces produkcji. Oparliśmy się na naszej wiedzy i doświadczeniu, analizując podobne wyroby, które produkowaliśmy w przeszłości. Wykorzystaliśmy dane z systemów CAM, które zawierały informacje o czasach obróbki na maszynach CNC, i uzupełniliśmy je o czas przygotowawczo-zakończeniowy (Tpz). Zaczęliśmy systematycznie mierzyć czas Tpz dla różnych typów wyrobów i na podstawie zebranych danych stworzyliśmy współczynniki przeliczeniowe, które uwzględniały specyfikę materiału, złożoność detalu i inne istotne czynniki.
Nasza wąska specjalizacja i ograniczona liczba typów produkowanych wyrobów pozwoliły nam stosunkowo szybko opracować skuteczny system szacowania czasów realizacji. Stopniowo chaos zaczął ustępować, a nasza produkcja stała się bardziej mierzalna i przewidywalna. Równolegle z tymi działaniami wdrożyliśmy nowe oprogramowanie do zarządzania produkcją, które było bardziej elastyczne i lepiej dostosowane do specyfiki naszej działalności. Rozbudowaliśmy je o własne aplikacje i moduły, które usprawniały jego działanie w różnych obszarach firmy.
Ograniczenie liczby zleceń – mniej znaczy więcej
Kolejnym krokiem w kierunku poprawy efektywności było ograniczenie liczby zleceń jednocześnie realizowanych na produkcji. Zastosowaliśmy zasadę „mniej znaczy więcej”, która zakładała, że lepiej skupić się na mniejszej liczbie zleceń i zrealizować je w terminie, niż rozpraszać zasoby na wiele projektów i generować opóźnienia. Określiliśmy nasze moce przerobowe w skali tygodnia i dziś wprowadzamy na produkcję tylko tyle zleceń, ile jesteśmy w stanie realnie wyprodukować, uwzględniając dostępne zasoby. Zmniejszenie ilości zleceń w toku pozwala nam lepiej monitorować procesy produkcyjne, identyfikować wąskie gardła i wprowadzać niezbędne korekty. Zniknęły kilkudniowe kolejki przed maszynami, a na niektórych stanowiskach zaczęło brakować zadań, co zmusiło nas do bardziej efektywnego planowania i przydzielania zasobów. Wydajność produkcji wzrosła. Więcej na ten temat można przeczytać na naszym blogu: https://toptechpolska.pl/gora-lodowa-produkcja-jednostkowa/ .
Nowa definicja efektywności w TOPTECH® – szersze spojrzenie
Wraz z wprowadzonymi zmianami, postanowiliśmy również zdefiniować na nowo pojęcie efektywności w naszej firmie. Zamiast skupiać się wyłącznie na czasie realizacji zamówienia od momentu jego otrzymania do momentu wysyłki, zaczęliśmy mierzyć wydajność produkcji, czyli czas od rozpoczęcia działań okołoprodukcyjnych związanych z wyrobem do momentu zakończenia wszystkich działań produkcyjnych. Ten czas można nazwać „cyklem produkcyjnym”. W niektórych przypadkach efektywność ta pokrywa się z wcześniejszą efektywnością realizacji zamówień, ale często jest krótsza, ponieważ uwzględnia tylko czas faktycznego procesu produkcyjnego, pomijając czas oczekiwania na start produkcji, na dostawę materiałów, i inne czynniki.
Dziś mamy dwa kluczowe wskaźniki wydajności/efektywności
- Efektywność czasu realizacji: Czas, jaki upływa od momentu wejścia zamówienia do firmy do momentu wysyłki gotowego wyrobu do klienta.
- Efektywność produkcji: Czas trwania cyklu produkcyjnego, czyli czas od wprowadzenia zamówienia do produkcji do momentu wyprodukowania gotowego wyrobu.
Planowanie okołoprodukcyjne – klucz do sukcesu
Wprowadzone zmiany znacząco usprawniły proces produkcyjny i umożliwiły nam precyzyjne sterowanie terminami realizacji. Nie wyeliminowały jednak całkowicie problemu opóźnień w dostawach. Dlatego postanowiliśmy wdrożyć dodatkowe działania okołoprodukcyjne, które miały na celu poprawę efektywności realizacji zamówień. Skupiliśmy się na optymalizacji produkcji od procesu ofertowania, przez skrócenie czasu przygotowania dokumentacji technicznej, usprawnienie komunikacji z klientami oraz poprawę logistyki wewnątrz firmy. Wdrożyliśmy system monitorowania postępu prac na każdym etapie realizacji zamówienia, co pozwoliło nam na szybką reakcję w przypadku wystąpienia jakichkolwiek problemów. O szczegółach tych działań opowiem w kolejnym wpisie na blogu.
Wnioski – czy warto było?
Podsumowując nasze doświadczenia, możemy z całą pewnością stwierdzić, że praca nad efektywnością w produkcji jednostkowej stempli, matryc i znakowników ma ogromny sens. Uzyskane efekty pokazują, że możliwe jest znaczne usprawnienie procesów produkcyjnych, skrócenie czasów realizacji zamówień i poprawa jakości wyrobów, nawet w środowisku, gdzie każdy detal jest unikalny. Trzeba jednak pamiętać, że efektywność w produkcji jednostkowej należy definiować i rozwijać inaczej niż w produkcji seryjnej.
Czy można nad nią panować i ją rozwijać? Jak najbardziej! Wymaga to jednak stopniowego działania, ciągłej oceny i modyfikacji wprowadzanych zmian oraz elastycznego podejścia do planowania i zarządzania produkcją. Jak to mówią, nie da się zjeść słonia na raz, ale małymi łyżeczkami i z odpowiednią strategią można osiągnąć sukces.
Czy warto poświęcać czas na przygotowanie danych o czasie realizacji i analizę procesów produkcyjnych? Na początku może się to wydawać nieopłacalne, ale w dłuższej perspektywie czas ten zwraca się z nawiązką. Zebrane dane i ustalone wskaźniki pozwalają na lepsze planowanie produkcji, podejmowanie trafnych decyzji i optymalizację systemu planowania produkcji. Ponadto, wiedza o procesie produkcyjnym przynosi korzyści w innych obszarach firmy, takich jak marketing, sprzedaż i obsługa klienta. Naszym zdaniem, inwestycja w analizę i optymalizację procesów produkcyjnych jest kluczowa dla osiągnięcia sukcesu w konkurencyjnym środowisku.